How To Weld Inconel
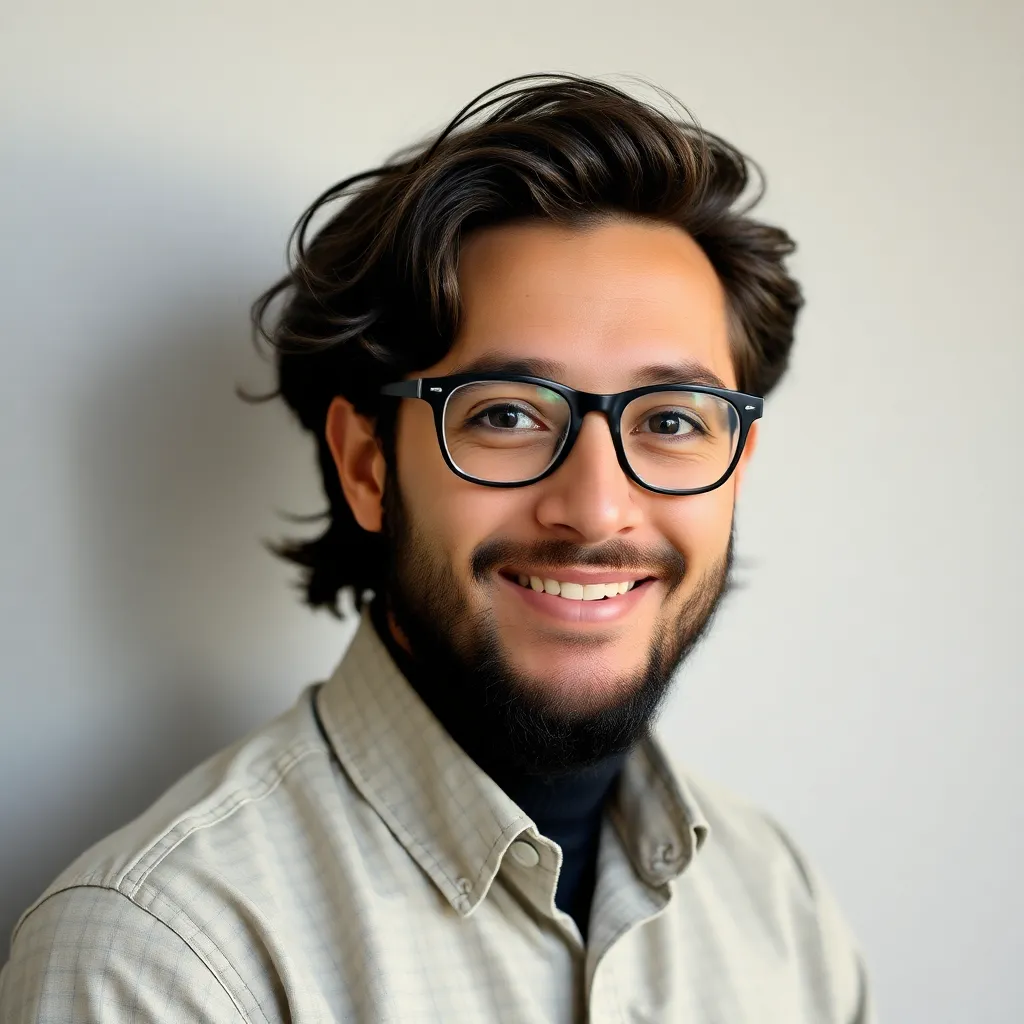
Ronan Farrow
Apr 16, 2025 · 4 min read

Table of Contents
How to Weld Inconel: A Comprehensive Guide for Welders
Inconel, a nickel-chromium-based superalloy, presents unique challenges for welders due to its high strength, resistance to corrosion and heat, and tendency to work-harden. This guide will walk you through the essential steps and considerations for successfully welding Inconel. Mastering this technique requires precision and adherence to proper procedures.
Understanding Inconel's Properties and Welding Challenges
Before diving into the welding process, it's crucial to understand the material properties that impact welding:
- High Strength and Hardness: Inconel's inherent strength necessitates the use of specialized welding techniques and equipment to avoid cracking.
- High Thermal Conductivity: This property requires careful heat input control to prevent overheating and subsequent distortion or cracking.
- Work Hardening: Inconel work hardens rapidly, meaning repeated deformation increases its hardness and makes further welding more difficult. This requires specific post-weld treatments.
- Susceptibility to Hot Cracking: This risk needs to be mitigated through proper preheating, interpass temperature control, and post-weld heat treatment (PWHT).
Essential Equipment and Materials for Inconel Welding
Successfully welding Inconel demands the right tools and materials:
- Specialized Welding Machines: GTAW (Gas Tungsten Arc Welding), often called TIG welding, is the preferred method due to its precise heat control. Consider machines with pulse capabilities for enhanced control. SMAW (Shielded Metal Arc Welding), or stick welding, can be used in certain applications but requires a skilled welder.
- Filler Metal: Choosing the correct filler metal with a matching chemical composition is paramount. The filler metal should be carefully selected to match the base Inconel alloy.
- Tungsten Electrodes: For TIG welding, use high-purity tungsten electrodes (e.g., 2% thoriated or lanthanated) to ensure consistent arc stability.
- Shielding Gas: High-purity argon is the typical shielding gas used in TIG welding Inconel. Maintain a consistent gas flow to prevent atmospheric contamination.
- Safety Equipment: Welding Inconel requires rigorous adherence to safety protocols, including wearing appropriate PPE (Personal Protective Equipment) such as welding helmets, gloves, and protective clothing.
Step-by-Step Guide to TIG Welding Inconel
This guide focuses on TIG welding, considered the best method for most Inconel applications:
1. Pre-Welding Preparation:
- Cleaning: Thoroughly clean the weld joint area to remove any contaminants like grease, oil, or oxides. Use a suitable cleaning agent and wire brush.
- Preheating (Often Necessary): Preheating the base metal to a specific temperature (varies depending on the Inconel grade and thickness) reduces the risk of hot cracking. This preheating temperature is critical and must be carefully controlled.
- Joint Design: Selecting an appropriate joint design (e.g., butt joint, fillet weld) impacts the welding process. A well-designed joint is essential for success.
2. Welding Procedure:
- Low Heat Input: Maintain a low heat input to prevent excessive heat build-up and distortion. This requires a slow, controlled welding speed.
- Proper Technique: Use a consistent arc length and weaving technique to ensure complete penetration and fusion.
- Interpass Temperature Control: Maintain the interpass temperature within the recommended range to prevent cracking. This often requires pauses between weld passes to allow the metal to cool.
3. Post-Welding Procedures:
- Cooling: Allow the weldment to cool slowly to minimize residual stresses and reduce the risk of cracking. Rapid cooling should be avoided.
- Post-Weld Heat Treatment (PWHT): Depending on the application requirements, PWHT may be necessary to relieve stress and improve material properties. This process involves heating the welded assembly to a specific temperature and holding it for a specified time, followed by slow cooling.
- Inspection: Inspect the weld for any defects, such as porosity, cracking, or incomplete fusion. Nondestructive testing methods (NDT), such as radiographic testing or ultrasonic testing, may be employed to assess the weld quality.
Advanced Considerations and Troubleshooting
- Tack Welding: Use small, controlled tack welds to hold the parts together before the main welding operation.
- Back Purging: In certain applications, back purging (introducing an inert gas behind the weld) may be required to prevent oxidation and improve weld quality.
- Troubleshooting: Address issues such as porosity, cracking, and undercut promptly. Understanding the root causes of these problems is crucial for corrective action.
Successfully welding Inconel requires a combination of skill, knowledge, and attention to detail. Always consult the specific welding procedures recommended by the Inconel manufacturer and adhere to stringent safety protocols. Remember that practice and continuous learning are crucial for mastering this challenging but rewarding welding technique.
Featured Posts
Also read the following articles
Article Title | Date |
---|---|
How To Use Rockwool | Apr 16, 2025 |
How To Train A Service Dog For Pots | Apr 16, 2025 |
How To Tow A Boat On The Water | Apr 16, 2025 |
How To Tell If Hardwood Floors Can Be Refinished | Apr 16, 2025 |
How To Tap Hardened Steel | Apr 16, 2025 |
Latest Posts
Thank you for visiting our website which covers about How To Weld Inconel . We hope the information provided has been useful to you. Feel free to contact us if you have any questions or need further assistance. See you next time and don't miss to bookmark.