How To Weld Spring Steel
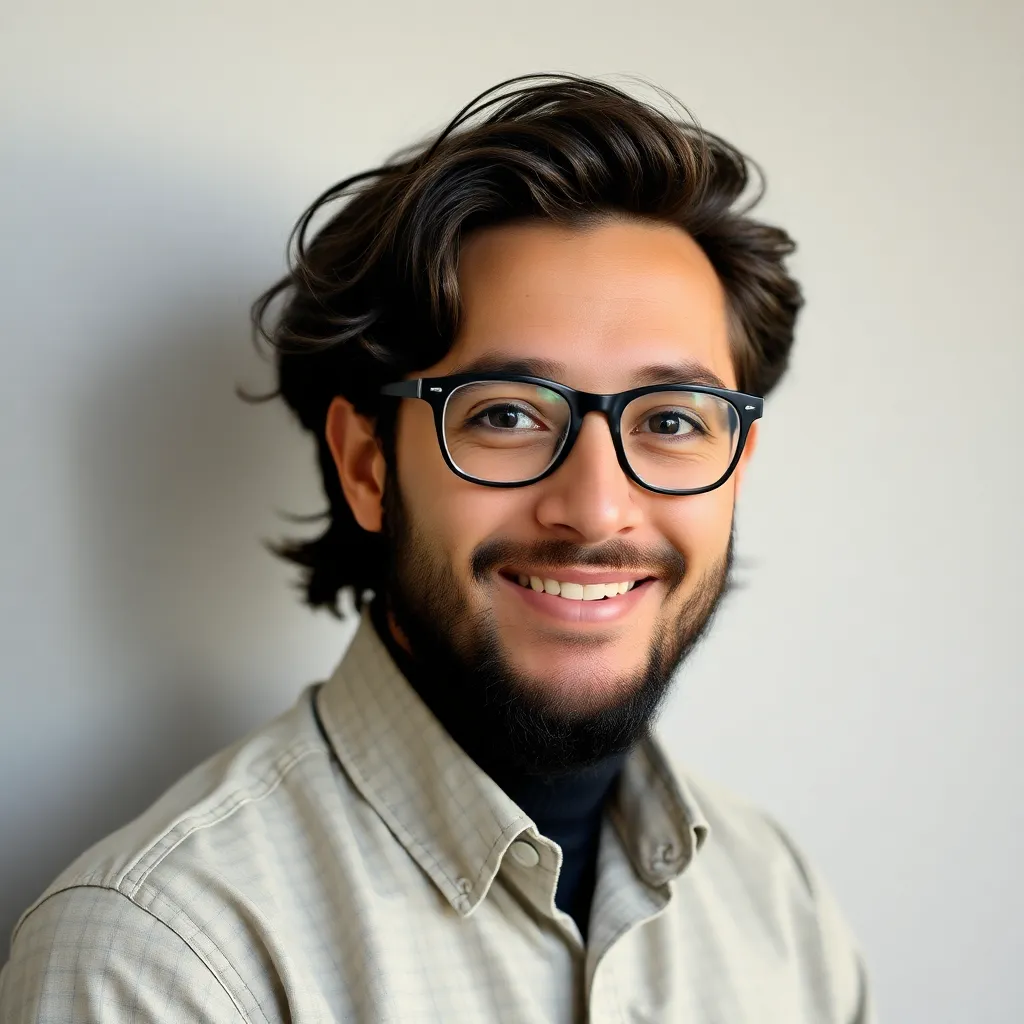
Ronan Farrow
Apr 16, 2025 · 3 min read

Table of Contents
How to Weld Spring Steel: A Comprehensive Guide
Spring steel is a high-carbon alloy steel known for its exceptional strength and elasticity. Welding it presents unique challenges due to its high hardness and tendency to warp or crack. However, with the right techniques and precautions, successful welds are achievable. This guide will walk you through the process, covering essential considerations and best practices.
Understanding the Challenges of Welding Spring Steel
Before diving into the welding process, it's crucial to understand the inherent difficulties:
High Carbon Content:
The high carbon content of spring steel contributes to its strength but also makes it prone to hardening and cracking during welding. The heat input from the welding process can cause rapid cooling, leading to a hardened, brittle zone around the weld. This area becomes susceptible to cracking under stress.
Work Hardening:
Spring steel is susceptible to work hardening, meaning it becomes harder and more brittle with repeated deformation. This characteristic impacts weldability, as the heat-affected zone can become excessively hard.
Distortion and Warping:
The high tensile strength of spring steel means it tends to distort and warp significantly during welding due to the uneven heating and cooling process.
Choosing the Right Welding Process
Selecting the appropriate welding process is paramount for successful spring steel welding. Several methods are suitable, each with its own advantages and limitations:
MIG Welding (Gas Metal Arc Welding):
MIG welding, using a short-circuiting transfer mode, is often preferred for its precise control over heat input. This minimizes the risk of overheating and cracking. Proper shielding gas selection (often argon or a mixture of argon and carbon dioxide) is crucial.
TIG Welding (Gas Tungsten Arc Welding):
TIG welding provides excellent control over the weld bead and minimizes heat distortion. It is often favored for smaller, more intricate welds. However, it requires more skill and precision compared to MIG welding.
Resistance Welding:
Resistance welding techniques like spot welding are suitable for joining thinner sections of spring steel. However, this method is less versatile than MIG and TIG welding for complex joints.
Essential Preparations for Welding Spring Steel
Proper preparation is crucial for a successful weld:
Preheating:
Preheating the spring steel to a specific temperature (usually between 200°F and 300°F, but consult the spring steel specification for precise details) reduces the risk of cracking by controlling the cooling rate. A consistent preheat temperature is crucial.
Cleanliness:
Thorough cleaning of the weld area is essential. Remove all dirt, grease, rust, and any other contaminants to ensure proper fusion. Use appropriate cleaning agents, paying particular attention to the edges of the joint.
Fixturing:
Securely clamping the spring steel in a jig or fixture minimizes distortion and warping during welding. The jig should prevent movement and provide stability during the heat cycle.
Post-Weld Heat Treatment:
Following the welding process, post-weld heat treatment (PWHT) can relieve residual stresses and improve the weld's ductility and toughness. The exact process will depend on the specific steel grade and the welding process used. This often involves slow cooling to avoid thermal shock.
Safety Precautions
Welding spring steel involves working with high temperatures and potentially hazardous fumes. Always wear appropriate personal protective equipment (PPE), including:
- Welding helmet with appropriate shade lens
- Welding gloves
- Long-sleeved shirt and pants
- Safety glasses
- Respiratory protection
Post-Weld Inspection
After welding, a careful inspection of the weld is critical to ensure integrity and quality. Look for:
- Cracks
- Porosity
- Undercuts
- Excessive distortion
If any defects are identified, corrective action may be required.
Welding spring steel requires skill, precision, and careful attention to detail. While challenging, understanding the properties of the material, selecting the correct welding process, and employing proper preparation and safety techniques will significantly improve your chances of achieving a successful and durable weld. Remember to always consult the manufacturer's specifications for your specific spring steel grade for detailed recommendations.
Featured Posts
Also read the following articles
Article Title | Date |
---|---|
How To Stay Cool In A Warehouse | Apr 16, 2025 |
How To Tune A 5 3 After Cam Swap | Apr 16, 2025 |
How To Worship Your Partner | Apr 16, 2025 |
How To Update Tivimate | Apr 16, 2025 |
How To Wire A Blower Motor To A Toggle Switch | Apr 16, 2025 |
Latest Posts
Thank you for visiting our website which covers about How To Weld Spring Steel . We hope the information provided has been useful to you. Feel free to contact us if you have any questions or need further assistance. See you next time and don't miss to bookmark.