How To Weld Stainless To Mild Steel
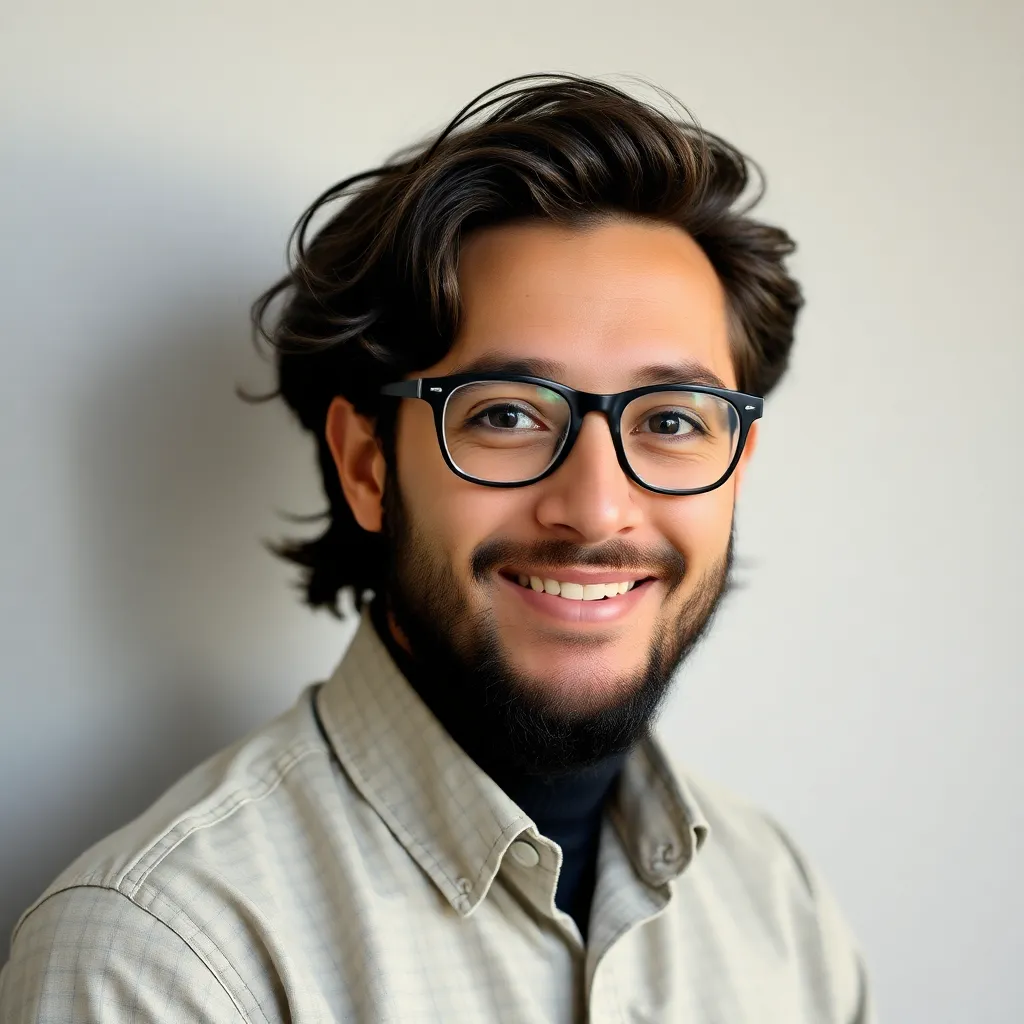
Ronan Farrow
Apr 03, 2025 · 4 min read
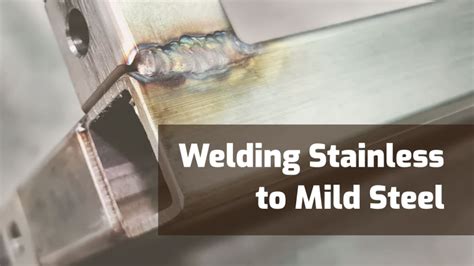
Table of Contents
How to Weld Stainless Steel to Mild Steel: A Comprehensive Guide
Welding stainless steel to mild steel presents unique challenges due to the dissimilar metallurgical properties of the two metals. Improper welding techniques can lead to corrosion, cracking, and ultimately, weld failure. This comprehensive guide will walk you through the process, emphasizing best practices to achieve a strong, durable, and corrosion-resistant weld.
Understanding the Challenges
Before diving into the welding process, it's crucial to understand why welding stainless steel to mild steel is more complex than welding similar metals. The key differences lie in:
- Chemical Composition: Stainless steel contains significant amounts of chromium (typically 18%) which forms a passive chromium oxide layer, providing excellent corrosion resistance. Mild steel lacks this protective layer, making it susceptible to rust and corrosion. This difference necessitates careful consideration of filler metal selection and welding parameters to prevent corrosion at the weld joint.
- Thermal Conductivity: Stainless steel has a lower thermal conductivity than mild steel, meaning it heats and cools slower. This difference can lead to uneven heat distribution during welding, potentially causing problems like cracking or porosity in the weld.
- Coefficient of Thermal Expansion: Stainless steel expands and contracts at a different rate than mild steel when subjected to heat. This difference can introduce residual stresses in the weld, increasing the risk of cracking.
Choosing the Right Welding Process
Several welding processes can be used to join stainless steel to mild steel, but some are better suited than others. The most common and effective methods include:
- Gas Metal Arc Welding (GMAW): Also known as MIG welding, GMAW offers good control over heat input and penetration, making it suitable for joining dissimilar metals. Pulse mode GMAW can be particularly advantageous, providing better control over heat input and reducing spatter.
- Gas Tungsten Arc Welding (GTAW): Also known as TIG welding, GTAW offers excellent control over heat input, making it ideal for precise welding and applications requiring a high-quality weld. However, it's a more complex and time-consuming process than GMAW.
Essential Considerations for Successful Welding
Regardless of the chosen process, several factors are crucial for achieving a successful weld:
1. Filler Metal Selection
Choosing the correct filler metal is paramount. You'll need a filler metal specifically designed for joining stainless steel to mild steel. These filler metals typically have a composition that bridges the gap between the two base metals, promoting a strong and corrosion-resistant weld. Always consult the filler metal manufacturer's specifications for compatibility and recommended welding parameters.
2. Pre-Welding Preparation
Proper surface preparation is essential for a high-quality weld. This includes:
- Cleaning: Thoroughly clean the surfaces to be welded, removing any dirt, grease, oil, or scale. Stainless steel should be cleaned with a suitable solvent to remove any surface contaminants that could negatively impact the weld.
- Grinding: Grinding the edges of the materials to be welded can help improve weld penetration and create a more consistent weld bead.
3. Welding Parameters
Optimizing the welding parameters is vital for achieving a strong and durable weld. These parameters will vary depending on the chosen process, the thickness of the materials, and the filler metal used. Experimentation and careful monitoring are key to finding the optimal settings. Consult your welding machine's manual and the filler metal manufacturer's recommendations.
4. Post-Welding Procedures
After welding, several post-weld procedures can improve the overall quality and durability of the joint:
- Heat Treatment: Depending on the specific materials and welding parameters, a post-weld heat treatment may be necessary to reduce residual stresses and prevent cracking.
- Inspection: Thoroughly inspect the weld for any defects like porosity, cracking, or incomplete penetration. Any imperfections should be addressed before proceeding with further applications.
Troubleshooting Common Issues
- Porosity: This is often caused by insufficient shielding gas coverage, contamination of the weld area, or incorrect welding parameters.
- Cracking: This can result from rapid cooling, high residual stresses, or improper filler metal selection.
- Corrosion: This can occur if the weld is not properly protected or if an unsuitable filler metal was used.
Addressing these issues requires careful attention to the welding process and meticulous attention to detail.
Conclusion
Welding stainless steel to mild steel requires skill and precision. By following these guidelines, carefully selecting your materials and meticulously controlling the welding parameters, you can achieve a strong, durable, and corrosion-resistant weld. Remember to always prioritize safety and consult relevant safety data sheets (SDS) before commencing any welding operations.
Featured Posts
Also read the following articles
Article Title | Date |
---|---|
How Are Bonuses Handled In Divorce | Apr 03, 2025 |
How Big Do Albino Plecos Get | Apr 03, 2025 |
Gr20 Corsica How Many Days | Apr 03, 2025 |
How Can You Tell If Your Chimney Is On Fire | Apr 03, 2025 |
Ghk Cu Powder How To Use | Apr 03, 2025 |
Latest Posts
-
How Hot Does A Roof Get In The Summer
Apr 04, 2025
-
How Hot Does A Powder Coating Oven Get
Apr 04, 2025
-
How Hot Does A Powder Coat Oven Get
Apr 04, 2025
-
How Hot Does A Harley Engine Get
Apr 04, 2025
-
How Hot Does A 250w Heat Lamp Get
Apr 04, 2025
Thank you for visiting our website which covers about How To Weld Stainless To Mild Steel . We hope the information provided has been useful to you. Feel free to contact us if you have any questions or need further assistance. See you next time and don't miss to bookmark.